No More Thermal Runaway Phenomena in Electric Car Batteries
South Korea’s safety standards for electric cars are heading towards global excellence. The recently opened Eco-friendly Automotive Parts Certification Center within the Gwangju Light Green National Industrial Complex on November 24, 2023, just two years after its establishment in 2020, is a testament to this progress. Its main responsibility is to address certification requests from manufacturers and provide post-management. Gyeonggi Province oversees overall safety, focusing on battery-electric vehicle-related tasks conducted here. This article provides an overview of the Eco-friendly Automotive Parts Certification Center and the current state of battery-related safety technology.
Battery electric vehicles have already gained worldwide popularity. They align with the global trend of addressing climate crises and ensuring energy security by supporting the booming renewable energy industry. In the third quarter of 2023, Europe saw a 50% increase, the United States witnessed a 62% surge, and China is expanding its presence in overseas markets despite a slowdown due to subsidy cuts. Even Japan, which strongly favors hybrids, experienced a 42% increase. Remarkably, South Korea was the only major country with a 28% decline in electric vehicle sales, highlighting the impact of policy directions on the industry.
Despite Hyundai Motor Group’s global success alongside Tesla, BYD, and others, it faces challenges in its domestic market. While its products are recognized worldwide, the local business environment hinders growth. This is due to setbacks in the renewable energy industry, especially the withdrawal of the one-time-use item policy, which contradicts global trends.
The Eco-friendly Automotive Parts Certification Center, operated by the Korea Transportation Safety Authority’s Automotive Safety Research Institute, consists of four test facilities: Battery Test Lab, Crash Test Lab, Impact Test Lab, and Fire Test Chamber. It possesses 26 evaluation equipment, including 6 eco-friendly automotive battery safety evaluation equipment, 11 collision safety evaluation equipment, 6 impact safety evaluation equipment, fire scene equipment, and legal auxiliary equipment.
Four out of eight Battery Test Lab rooms are equipped with explosion-proof structures to prepare for battery fires and explosions. They have installed vibration, impact, immersion, and compression testers to evaluate safety in battery immersion and even a large fire test chamber for simulating electric bus fires.
The Eco-friendly Automotive Parts Certification Center conducts enhanced evaluation tests for 12 criteria, surpassing the international standard of 10 criteria, including battery impact tests. These tests cover thermal safety, electrical safety, chemical safety, and physical safety, such as thermal shock tests, short circuit tests, overcharge tests, over-discharge tests, overheat prevention tests, overcurrent tests, penetration tests, impact tests, compression tests, and drop tests.
For instance, the immersion test involves submerging an electric vehicle’s battery in water to test whether it ignites. This is not an internationally standardized procedure, and some countries do not consider it necessary due to cultural differences. However, China has recently added it to its requirements, and Europe and the United States are considering similar additions.
Submersion Test and Drop Impact Test Contribute to Globalization
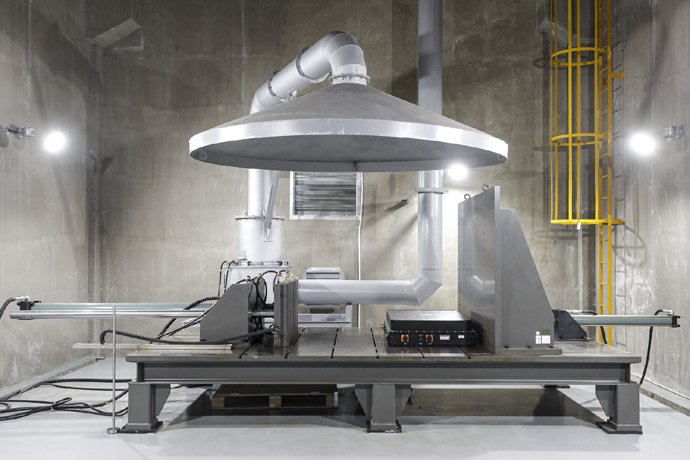
The Eco-friendly Automotive Parts Certification Center has contributed to global harmonization by incorporating battery drop impact tests into safety standards and adopting recommendations for sunroof safety enhancements. This has elevated South Korea’s international status in automotive safety technology.
Regarding battery fires, the center has developed numerous countermeasures. Since 2018, there have been approximately 80 electric vehicle-related fires in South Korea, with 10 occurring after collisions. The Automotive Safety Research Institute aims to develop world-class fire safety technology through electric vehicle safety assessments and integrated safety management technology.
Fire safety is being addressed in various scenarios, including driving, post-collision, and parking situations. Notably, preparations are being made for fires that may occur while the vehicle is parked. When the ignition is turned off, all the vehicle’s computers cease operation. Therefore, the center is developing technology that can detect fires or provide safety alerts even when the Electric Vehicle Battery Management System (BMS) is turned off. This pioneering effort is expected to be enforced as a safety standard from 2024.
Furthermore, technology is being developed to prevent thermal runaway, a concern during the early stages of electric vehicle adoption. LG Energy Solution, Hyundai Motor, and others have announced advancements in this area. Previously, there was no ultimate solution to extinguish fires until all the battery cells were consumed once one cell ignited. However, the Eco-friendly Automotive Parts Certification Center has conducted various experiments to address this issue. South Korean battery companies, which mainly use NCM batteries that are relatively vulnerable to fires compared to LFP batteries, must tackle this challenge.
The center recently demonstrated experiments involving battery ignition using a self-funded battery. In contrast to typical gasoline experiments, they used LPG gas for combustion, which reaches temperatures of 800 to 1,100 degrees Celsius. They monitored the ignition and transition status of the battery for 2 minutes and 30 seconds. On the day before the center’s opening, they conducted a shortened experiment of 60 seconds. Although there were ignition events in some battery cells when the fire was extinguished, they quickly subsided. After approximately 30 minutes following the experiment’s conclusion, it is possible to confirm whether there will be a full ignition or explosion. In essence, they have reached a technological level where they can effectively suppress the previously mentioned thermal runaway phenomenon.
As for battery fires in electric vehicles, current best practices involve cooling with water mist. Although suggestions exist to cover the battery with a lid to prevent air circulation, this approach has not been verified.
The Eco-friendly Automotive Parts Certification Center conducts experiments with purchased batteries at its own expense. The laboratory contains battery packs from Korean companies like LG Energy Solution and international manufacturers such as CATL and BYD.
In addition, they are pushing for a pre-certification system, unlike finished vehicles and other parts that self-certify. This means a two-stage safety verification process, allowing for a different allocation of responsibilities and potentially more proactive safety enhancements.
Of course, there are other aspects where safety needs to be ensured. The Eco-friendly Automotive Parts Certification Center aims to develop world-class technology and lead safety testing in the era of electric vehicles.
The Crash Test Lab offers various tests to evaluate the collision safety of eco-friendly vehicles, including vehicle-to-vehicle collision tests and tests that achieve collision speeds of 100 km/h for vehicles with a total weight of 3.5 tons or less.
When hydrogen fuel cell electric vehicles were first introduced, Germany established safety regulations, including drilling holes in the vehicle chassis to prevent gas accumulation and prohibiting the parking of hydrogen vehicles in underground parking lots. However, despite the passage of several years since the start of electric vehicle sales in South Korea, there are no regulations or standards regarding safety issues in apartment underground parking lots and other areas. Given the irreversible nature of the electric vehicle era, there is an urgent need for more comprehensive regulations to prepare for its expansion.
By. Chae Young Seok
Most Commented